Strategy and goals
Strengthening our position as a turnkey provider in the core automotive business through forced digitization
With its diversified customer portfolio, the EBZ Group is excellently equipped to face the requirements and challenges of its core automotive business. This includes the digital twin of a production plant that ranges from the creative process to a digital image and virtual commissioning. This digitization has been one of the keys to our success for years now and among the core competencies of the EBZ Group.
This is why we force digitization projects in our enterprise to respond to ever increasing demands more effectively and with greater precision. The focus here, including in terms of investment, is on the optimizing and innovative redesign of existing processes. Rather than relying on solutions from external service providers and software companies in this respect, we strike out in new directions to exploit potential to the full. From A for artificial intelligence to Z for Z-programs in SAP, we possess the professional and technical expertise within the Group that develops and implements our own smart solutions.
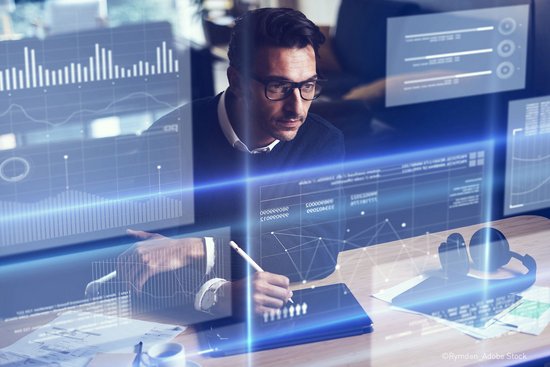
Growth and diversification, for and with sustainability
The strong positioning through diverse abilities and skills described previously, and the options presented by a variety of materials will enable the EBZ Group to penetrate into further business segments and product areas in future. Complex series products, such as high-performance EBZ electrolysis blocks and, also, modular products with a higher engineering component such as high-performance battery systems for buses, trains, maritime and stationary applications will in future be an important part of the EBZ service portfolio. One significant step in this regard is the establishment of EBZ nano power which will help the EBZ Group to achieve a strong position in growing and sustainable markets.
In addition, the EBZ Group pursues its own clear CO₂ reduction targets. Next to the societal obligation, we view this as an opportunity to invest in the future and pursue the clear goal to proactively monitor risks, such as security of supply, ever increasing energy costs and the increase in regulation, and to minimize these. We aim to achieve complete CO₂ neutrality in production by 2030 in our German locations.
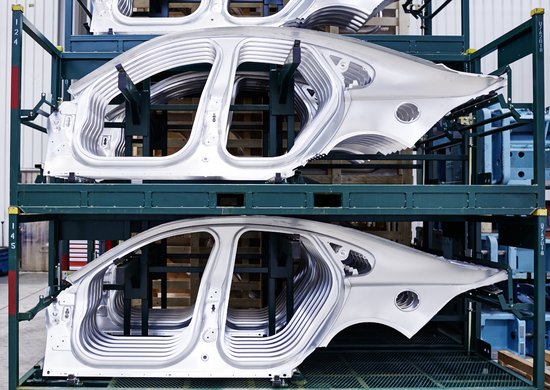
Employees
The EBZ Group employed a total of 1,767 personnel in 2021, with 975 of these at the locations in Germany, 516 at the European locations and 276 at the locations outside Europe.
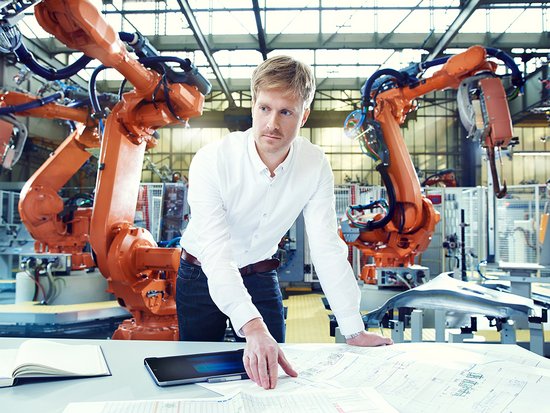
Facts, figures, and data
In addition to EBZ SE, the holding and parent company located in Ravensburg, the EBZ Group consists of 12 operational subsidiaries. In terms of countries and markets, the EBZ Group is represented in Germany at three locations in Ravensburg, Ammerbuch (near Stuttgart), and Schemmerhofen (near Biberach) and through subsidiaries in China, the UK, India, Poland, the Czech Republic, Hungary, and the United States. However, it also works for its customers outside these countries and markets.
Performance figures/Operating equipment
- Factory planning and simultaneous engineering (SE) specialist
- Planning, design, and simulation of everything from complex production systems to the digital factory
- BIW joining systems
- Battery assembly systems
- Fuel cell assembly systems
- Powerful engineering business with over 500,000 own service hours
- Design know-how realized in Siemens NX or CATIA V5
- All reputable factory planning and robot simulation tools
Innovative, flexible, and versatile production systems for applications ranging from small systems to entire bodies
- Leading integrator: 1000 robots/annum
- Global positioning in EU, USA & China
- Digital twin (virtual commissioning)
- Own process expertise with technical center
- High-speed materials handling
- Smart roller hemming head & roller cleaning device
- Modular framing system
- Own laser cabins
- Smart component supply & feeder magazines (LCA)
- Conception, development, design, production, and commissioning of individual and customized assembly systems
- Variable linking of individual stations to form complex assembly systems
- Centralized programming and control using the latest PLC systems
- Virtual commissioning
Portfolio:
- Marriage lines
- Fitting of windows and glass roofs
- Wheel and axle assembly
- Cockpit installation
We develop, design and supply complex systems for the assembly of energy storage systems.
- Planning, design, and implementation of process-reliable automated assembly systems for batteries
- Adaptation of degree of automation, cycle times and output volumes to suit customer specifications
Portfolio:
- Module and cell block assembly
- Battery pack assembly (automotive)
- High-voltage battery assembly in the vehicle
- Fuel cell stacking systems
- MEA assembly
- Integration of individual technologies (EOL, helium test, HV test, plasma cleaning…)
- Material flow simulation
- Planning of process, output & availability of the overall system
We give shape to vehicle designs.
- 160,000 in-house engineering hours
- The largest non-OEM license holder in Europe with 20 AutoForm licenses
- Method planning and simulation specialist for complex forming dies
- Feasibility
- Series method planning
- Kickback analysis and compensation in outer skin quality
- Simultaneous engineering specialist
- 90 own Catia design stations
- 55 own Siemens NX design stations
- Own Exporit foundry pattern making
Prototype tool manufacture for production of complete prototype bodies
- Prototype and small series production in steel, aluminum and high-strength materials
- Extensive know-how in different manufacturing processes and joining technologies
- Hot-formed prototype components
- Part production for classic cars
- Automotive industry safety standards
- EN ISO 9001; EN ISO 14001; TISAX label
- 100% own value chain
- Engineering: AutoForm, CATIA V5, Siemens NX
- Mechanical processing up to 6000 mm
- 8 presses up to 5000 mm
- 2 fluid cell presses
- Trumpf laser systems up to 4000 mm
- Optical and tactile measuring technology up to 5500 mm
- Laser welding and laser hardening
- Electric chamber furnaces up to 4000 x 1800 x 650 mm
Specialist for outer skin and complex structural components:
- 180 large-scale molds
- 70% outer skin & 50% aluminum parts
- Conception and design
- Kickback compensation
- Heavy-duty mechanical machining with HSC
- Heat treatment vacuum furnace / Laser hardening / Inductive hardening
- Assembly capacity with 8000 m² floorspace with cranes
- Measurement technology with BlueRay scanning and tactile measurement system
- Laser powder build-up welding
- Precision grinding of cutting blades
- 15 try-out presses up to 2,500 tonnes
- 14 of these with 5 m table
- 2 of these with servo-mechanical presses
- 11 of these hydraulic & 4 mechanical
Manufacture of components and realization of FRP assemblies in aerospace, automotive and industrial applications up to truck size
- Materials: CFRP, GFRP, APP monolithic or sandwich structure in each case with aviation certification where necessary
- Processes: fiberglass molding, vacuum presses, autoclave or injection processes, rapid prototyping in ULTEM™ 9085
- In-house design (Catia V5)
- Mold making: manufacture of single or multi-part molds made of CFRP or GFRP for producing FRP series components
- Model making with 5-axes machining of PU, epoxy, foam, wood, and similar.
- Job order production of FRP components, plastic plate materials, foam, laminated fabric, wood, and similar, dimensions up to 2800 x 1800 x 800 mm