Method planning & simulation
We lay the cornerstone for high component quality in conjunction with process-reliable parts production in your production facilities. Naturally enough, we also exploit our expertise here in our own toolmaking facility and press plant (familiarizing and try-out).
We map the entire production sequence virtually, from creation of initial concepts and drawing systems and detailed methodical planning with comprehensive forming simulation of all tool stages to calculation of the theoretical springback and resulting compensation. The focus here is on robust process design to maintain the stability of the manufacturability and dimensional accuracy of components for the entire production duration. We ensure this through the use of a variety of CAD/CAE and simulation software (e.g. Catia V5, Siemens NX or AutoForm).
It is very important to us that resources developed by EBZ enable sustainable production that conserves resources. This is why we work from the outset to maximize utilization of material while simultaneously ensuring a high level of component quality.
When it comes to challenging issues relating to manufacturability, we develop detailed optimization proposals with our customers and validate these through simulation.
To achieve a dimensionally accurate individual part, we in engineering focus intensively on the investigation of springback and its compensation. True to the motto “as much as necessary, as little as possible”, we endeavor to offset elastic springback effects in the operation sequence through targeted compensation measures. What is essential and of the highest priority here is the initial sheer line and surface appearance of outer skin components and fields of vision.
Finally, we create CAD surfaces suitable for milling for 3D processing of all tool shape components. This means that you receive everything from a single source, from early feasibility and method investigations to series production milling data processing.
Each of the services mentioned below can also be ordered as an individual scope. We would be more than happy to compile an appropriate offer for you.
Feasibility studies
- Manufacturability investigations for studies for cold and hot-formed sheet metal parts
- Simulation and robustness analysis with different AutoForm software modules
- Early phase of concept method planning and tool design
- Simultaneous engineering (SE)
- Handling of large-volume projects with an emphasis on project management aspects such as the deadline, quality and costs
Method development and manufacturability investigation
- Manufacturability and drawing system investigations in AutoForm
- Series method planning in the Catia V5 and Siemens NX systems
- Defining of production sequences and their working content in consultation with our workshop experts
- Consideration of technical conditions in customer press plants
- Simulative mapping of forming sequence in AutoForm
- Robustness analysis in AutoForm Sigma
- Detailed development of component change suggestions in CAD with validation through AutoForm
- Sheer line analysis and its risk assessment for outer skin components
- Definition of functional tool surfaces at an early planning stage
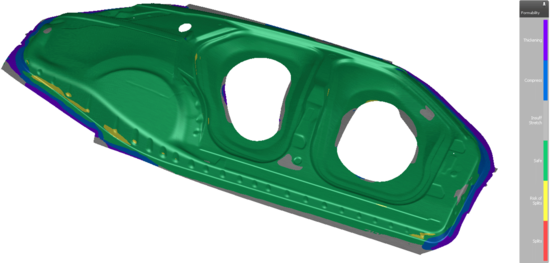
Springback simulation and springback compensation
- Springback analysis according to series method plan
- Investigation of parameters for dimensional component results
- Inspection of component position for each tool operation
- Development of compensation strategies in AutoForm Compensator
- Creation of bending rules for targeted surface modification in CAD
- Comprehensive documentation of compensation procedure and results
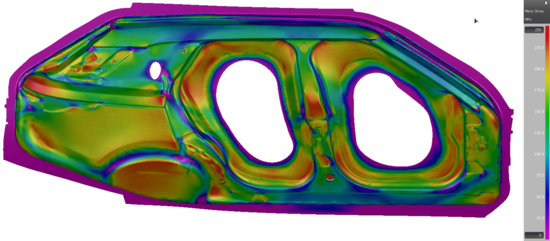
Active surface design
- Definition of active surface measures for try-out optimization
- Design of 3D active surfaces in CAD as a basis for subsequent CAM programming
- Creation of 3D active surfaces for tool correction based on dimensional deviations of physical components
Your contact
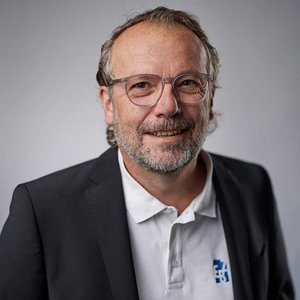