Tool design
Constructive designs are realized in close coordination with method planning, production, assembly, the press plant and the operating company.
To ensure the highest level of design quality, all tools undergo a separate quality check during which kinematic tool sequences are examined. The highest priority is given to collision-free and technically flawless tools. We commence with a detailed examination of mechanization conditions (DLP) during method design to assure smooth transportation of parts within the tool set in your press plants. The free movement of mechanization components relative to the tools is checked and optimization measures defined in parameterized press simulation models. All of this always occurs while taking the number of strokes required by the operator into account. We also take charge of detailed design of part mechanization (TMZ) if required. Our focus is on the design of stage sets for the manufacture of large tools, both for one’s own toolmaking facility and external customers.
In addition to standard modules for tool design in Catia V5 and Siemens NX, we also use other special tools such as PLS simulation to meet your requirements in every respect. Each of the services mentioned below can also be ordered as an individual scope. We would be more than happy to compile an appropriate offer for you.
Overview of services
- Design of sheet metal forming tools in the Catia V5 and Siemens NX systems
- Primarily multi-stage tool sets for sets for the manufacture of large tools (e.g. sidewall frames, fenders, doors, roofs, etc.)
- Profound expertise with regard to specific customer standards, design guidelines and press lines of numerous OEMs and tier suppliers
- Detailed calculation of required tool design for each operation stage, taking pressing conditions into consideration
- Support and handling of comprehensive design projects around the world, including project management
- Detailed depiction of tool kinematics during the press stroke
- Visualization and simulation of functionally relevant movements of tool components (e.g. slides, holding-down devices, blank holders, etc.)
- Identification and elimination of potential collisions in the tool sequence in the design phase
- Simulation of the installation and removal of particular items (e.g. slides, holding-down devices, attachments)
- Creation of flowcharts depicting component transport between press stages, taking mechanization technology and the press ram position into consideration
- Positioning of pneumatic transport suckers on the component
- Creation of mechanization system envelope volume relative to the number of strokes taking interference contours in the tool design into consideration
- Press run simulation based purely on 3D method data to full part transport scenarios taking tool design and press mechanization are possible
- Flowcharts possible in PLS and Catia V5 systems
- Certification available for creation of BMW flowcharts
- Design of component transport systems such as sucker beams, crossbars or robot mechanization
- Detailed depiction of position and connection of transport suckers to the mechanization system
- Simulation of overall kinematic press/tool/mechanization for maximum productivity and output
Kinematic tool simulation
- Detailed depiction of tool kinematics during the press stroke
- Visualization and simulation of functionally relevant movements of tool components (e.g. slides, holding-down devices, blank holders, etc.)
- Identification and elimination of potential collisions in the tool sequence in the design phase
- Simulation of the installation and removal of particular items (e.g. slides, holding-down devices, attachments)
Pressing run simulation
- Creation of flowcharts depicting component transport between press stages, taking mechanization technology and the press ram position into consideration
- Positioning of pneumatic transport suckers on the component
- Creation of mechanization system envelope volume relative to the number of strokes taking interference contours in the tool design into consideration
- Press run simulation based purely on 3D method data to full part transport scenarios taking tool design and press mechanization are possible
- Flowcharts possible in PLS and Catia V5 systems
- Certification available for creation of BMW flowcharts
Design of mechanization accessories
- Design of component transport systems such as sucker beams, crossbars or robot mechanization
- Detailed depiction of position and connection of transport suckers to the mechanization system
- Simulation of overall kinematic press/tool/mechanization for maximum productivity and output
Your contact
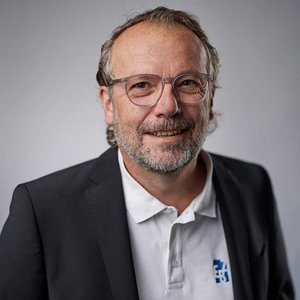